THE AUTOMOTIVE WORLD IS EVOLVING FASTER THAN EVER: GATES IS LAUNCHING NEW PRODUCTS AND SERVICES TO MEET THESE NEEDS
Ever changing powertrain trends require - higher efficiency, lower emissions and improved performance from Internal Combustion Engines – (ICE), over the last 5 to 10 years, stricter country specific emission legislations is one of the reasons leading to an increase in hybrid and full electric vehicles from vehicle manufacturers
INTERNALCOMBUSTION ENGINE HYBRID ELECTRIC
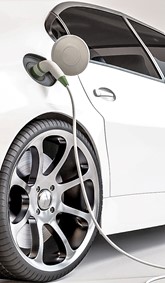
These evolving powertrain trends have led to major vehicle architectural changes, requiring more complex cooling systems to ensure correct vehicle operation.
Internal Combustion Engines (ICE) require various hoses and modular hoses to allow coolant to flow around the cooling system to enable the engine to operate at the correct temperature, heat generated in the engine from the combustion process is transferred into the coolant which circulates around the system – some of this heat transfer is used to heat the inside of the vehicle, the majority of heat is transferred to the main radiator which dissipates the heat into the atmosphere.
Hybrid vehicles also utilize an (ICE) engine along with electric motor(s), engines used in hybrid vehicles may also use some of the same hoses and modular hoses from their (ICE) only - vehicle family, however extra cooling hoses may also be incorporated into the cooling system for battery and electric motor cooling.
Battery Electric Vehicles don't have an (ICE) therefore we would presume vehicles using this architecture don’t require as many hoses or modular hoses? How wrong are we to presume this! battery electric vehicles use more coolant hoses than an (ICE) engine due to complex cooling systems used for battery and electric motor(s) cooling.
- Examples Of Power Train Technology Showing Hose Layout & Quantity:
INTERNAL COMBUSTION (ICE)
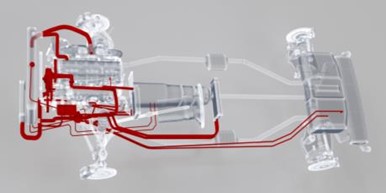
MILD & FULL HYBRID
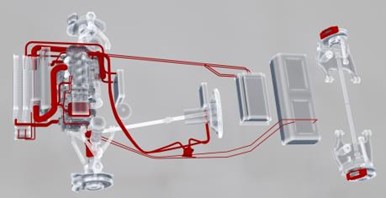
BATTERY ELECTRIC (BEV)
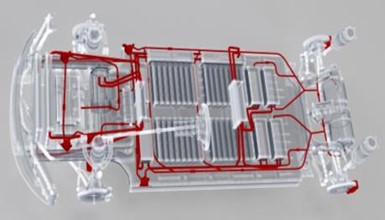
- OEMS ARE SHIFTING TO FULLY INTEGRATED THERMAL MANAGEMENT SYSTEMS ON EVS
- Increased Hose Complexity and Quantity
- Increased routing for regional heating and cooling needs
- Increase in integrated components (couplings, sensors, valves, flow restrictors)
- Improved assembly line efficiency
- Precision assembly and orientation
- Average of 15 hoses per vehicle on EVs
- Longer Hose Runs
- New manufacturing requirements
- Larger flow requirements
- Long lengths subject to more vibration
- Reduced weight requirements
- Continuous System Operation
- Use during driving and charging cycles
- Constant pressure vs. impulse operation
- Average of 15 hoses per vehicle on Bev’s: Longer Hose Runs over 13 ft. (4 meters) long
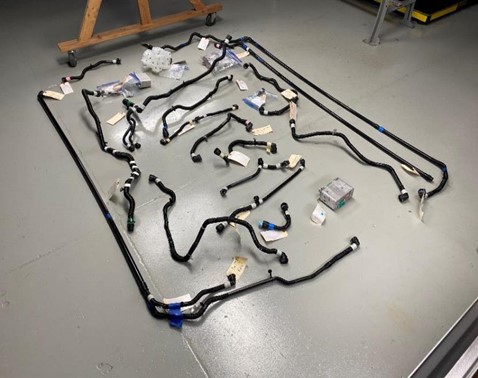
- Hoses and Lines are Key to Thermal Management Systems
In electric vehicles, batteries deliver maximum efficiency operating within the temperature range of (20˚- 40˚C) (68˚- 104˚F). Hoses and lines make sure the different media ─ oil, water, gases and air ─ are moved in the most economic way to reach the perfect balance of comfort, performance and mileage. This requires a sophisticated thermal management system. The hose and pipe systems are correspondingly complex. The lines for the battery cooling system in hybrid and electric cars laid in the underfloor section of the vehicle are up to 13 ft. (4 meters) long. Hoses and lines ensure the units maintain the proper operating temperature in both hot and cold conditions, allowing the batteries to operate at optimal efficiency and achieve maximum battery life.
As the automotive (ICE) evolves into Battery electric vehicles (BEV) the materials used to produce these vehicles has also evolved. This material evolution has seen more modular coolant hoses manufactured from thermoplastic materials and quick connector couplings, compared to EPDM rubber hoses used for internal combustion engines (ICE).
- Coolant lines with nylon straight and convoluted
- Quick connect couplings
- Thermoforming
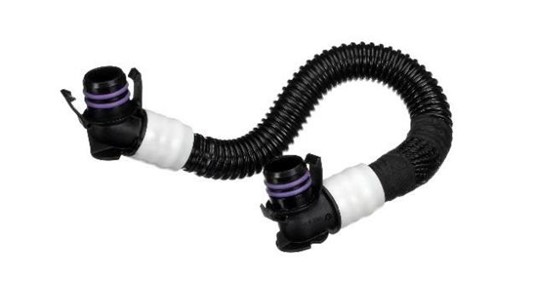
BEV cooling systems:
Battery technology has evolved allowing greater battery output with less frequent charging cycles required, battery stability and safety are key factors engineers have to consider when designing BEV cooling systems.
Battery Electric Vehicles (BEV) Batteries:
When an BEV battery charges or discharges, heat is generated, from both cycles, the amount of heat generated, depends on the rate of the charge or the discharge. lithium-ion batteries are generally used for BEV vehicles.
BEV batteries are designed to operate at ambient temperature, between (20°C to 25°C) (68°F to 77°F) controlling the battery temperature, helps to improve battery performance and operating life.
- During operation, these types of battery can withstand temperature ranges between (-30°C to 50°C) (-22°F to 140°F)
- During recharging, these types of battery can withstand temperatures ranges between (0°C and 50°C) (32°F and 122°F)
How Important Is A (BEV) Cooling System??
As mentioned previously batteries generate heat during their operating cycles – (charging or discharging cycles). It is important the battery temperature is constantly monitored and controlled, therefore an effective cooling system is essential for Battery Electric Vehicles (BEV).
High temperatures cause battery electrons to exit, which decreases voltage between both sides of the battery, batteries are designed to operate within a temperature range of approx. (20°C to 40°C) (68°F to 104°F) the temperature difference in the battery pack should ideally be maintained within approx. (5°C) (41°F)
Thermal runaways can occur at high temperature ranges (70°C and 100°C), (158°F and 212°F) which can destroy the battery pack
Thermal stability issues such as excessive internal temperature differences can lead to a difference in the rate of charge or discharge per cell, if the battery overheats its performance will be effected, battery fires and explosions may also occur.
During fast charge cycles the batteries receive high current loading from the charging equipment, generating excessive heat which requires extracting away from the batteries, ensuring the charging rate is maintained without overheating occurring.
Many DC charging system suppliers now exist, that manufacture home charging systems through to commercial charging systems. These systems appear to have charging capacity from 0kwh to over 350kwh for Extreme Fast Chargers (XFCs). Therefore these companies can advise and tailor what type of charging system is best for your personal requirements.
There are also occasions when the batteries require heating up, when the battery temperature is too low or too boost battery performance. Cells can not be charged below (0°C) (32°F) some BEV manufacturers utilize battery pre-heating in some models to enable high performance from 0 to 60 mph in less than 2 seconds.
As mentioned previously an effective cooling system is essential for Battery Electric Vehicles (BEV). Gates offers a vast range of modular cooling hoses for BEV Hybrid & ICE vehicles.
Gates has impressive market coverage for BEV Hybrid & ICE vehicles within it’s product range/portfolio.
Electric vehicle cooling hose products market coverage.
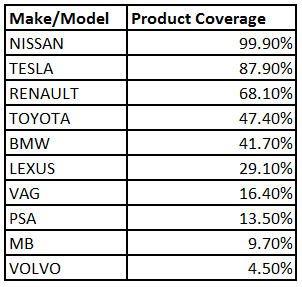
Please use Gates Electronic Online Catalogue Web Link to Gates Autocat, to check vehicle application, and cross reference information
https://gatesautocat.com/