A recent analysis of Gates claims data confirms that approximately 80% of all claims relating to water pumps (WPs) are a result of failure to follow the recommended installation procedures.
- Just over 50% of these claims are related to ‘coolant’ in general: mixing different types of coolants, not flushing the system correctly, use of tap water as a dilutant instead of distilled/deionized water
- Just under 30% of the claims are the result of improper use of sealant on WPs, which were already supplied with either a gasket or rubber O-ring
The combination of all these leads to WP failure, caused by continuous leakage from the most sensitive WP component - the mechanical seal.
Clearly, all these claims could have been avoided. The response from Gates is to produce a video that focuses on the fitting procedure and explains how to install a WP correctly.
This article looks in more detail at the installation procedure and explains how a damaged mechanical seal causes leakage and eventual premature WP failure.
1.The mechanical seal
Look at Fig.1. A mechanical seal generally consists of two seals/rings:
- Static seal/ring
- Dynamic seal/ring
Fig. 1
The static seal assembly is fixed into the WP housing and does not rotate (= static). However, spring pressure enables it to move along the axis of the bearing/impeller shaft. A combination of spring force and hydraulic pressure from the sealed coolant, ensures the seal faces are pushed together. This prevents leakage between the shaft and the WP housing. The dynamic seal assembly is secured to the shaft. Therefore, the dynamic seal rotates with the pulley-driven shaft.
2. Why the mechanical seal is such an important and sensitive component
Both the static and dynamic seal faces are precision machined to strict manufacturing tolerances to achieve a high quality of flatness.
Inside the assembly, both seal faces are pushed together. If the seal faces were rotated against each other in a dry condition, without any form of lubrication, they would be subject to wear and would quickly fail. This would be caused by the combination of face friction and heat generation
(see Fig .2).
A film of coolant, between the dynamic and static seal prevents face friction and heat generation and must always be introduced before WP operation. This film creates a micro-gap, which is maintained by the spring and hydraulic forces pushing the seal faces together, while the pressure of the liquid coolant between the seal faces (the fluid film) acts to push them apart.
This film of coolant provides lubrication and allows cooling between the seal faces. At the same time, it also ensures a perfect seal between the static and dynamic rings. This is very like the oil film that’s formed between the engine’s cylinder wall and the piston rings.
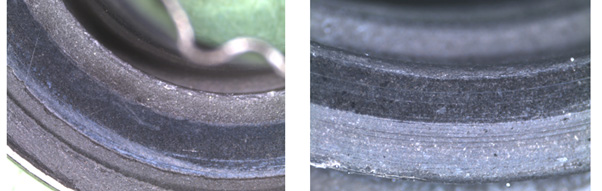
Fig.2
3.Creating a film of coolant to protect the mechanical seal
Remember that a film of coolant (micro-gap) must always be present to protect the mechanical seal surfaces from face friction and heat generation.
Resist any temptation to spin the impeller on the WP, once it’s been taken out of the box. Any attempt to dry-run a new WP will lead to rapid mechanical seal failure.
There are two ways to create a film of coolant:
- Submerge the new WP, impeller-side downwards, into a clean container of coolant that’s been recommended by the vehicle manufacturer (never re-use old coolant, because any particles or contaminants that may be present will cause premature failure). Rotate the WP pulley about 10 times by hand, to allow the film of coolant to be drawn between the faces of the mechanical seal
- Alternatively, when installing the new WP on the engine, refill the cooling system with the new coolant. The WP can then be rotated about 10 times by hand, to allow the film of coolant to be drawn between the faces of the mechanical seal
Failure to introduce the film of coolant liquid before checking the impeller for free movement will compromise the mechanical seal, with devastating consequences even before the WP has been installed. This will soon cause wear, rapid seal failure, resulting in continuous leakage during operation.
4.Draining and refilling cooling systems
Before fitting a new WP, fully drain the cooling system and ensure all contamination such as rust, scale and any other solid particles that may be present have been removed.
This can be achieved safely and efficiently with a Gates PowerClean (R) Flush Tool 91002. It delivers a controlled but powerful regulated flow that removes contaminants without damaging any components.
If the cooling system has not been fully drained and flushed, the new coolant will mix with the old coolant as well as any contaminating particles already present.
5.Types of contaminants
Solid particle contamination as small as 50 microns (.05mm) can cause irreversible damage to the seal surfaces (see Fig.3). Once the seal face has been damaged, any score marks will act as leakage paths (see Fig.4). These paths will allow coolant to continuously leak from the WP’s weep hole, into the weep hole chamber reservoir. Once the reservoir is full, leakage from the weep hole chamber vent hole will occur.
The weep hole is a small, drilled hole, usually found at the lowest point on the WP when in the mounted position. A small amount of coolant leakage from the weep hole is normal, particularly at start up, following installation. Many WPs (note: not all WPs will have one) have ‘weep hole chambers’. These are designed to catch and evaporate this coolant. If a large amount of coolant is leaking, an internal seal has failed. The WP requires replacement.
Discoloured coolant bleed marks around the weep hole and on the WP body itself are signs that the mechanical seal has failed due to some form of contamination.
See also: https://www.gatestechzone.com/en/problem-diagnosis/cooling-system/water-pump-failure- signs
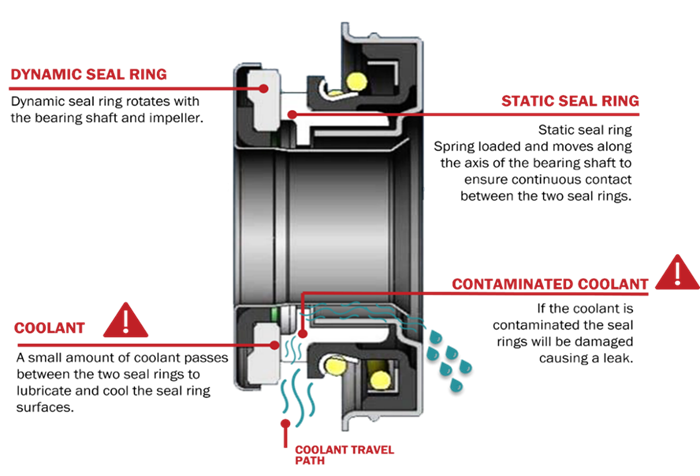
Fig.3
Particle contamination damages the mechanical seal faces, creating score marks that act as leakage paths. A direct result is continuous leakage from the weep hole during operation.
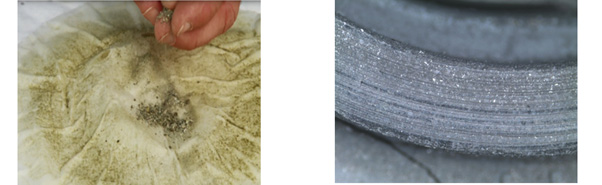
Fig.4
Products used to stop cooling system leaks, may cause irreversible damage to mechanical seals on WPs. That’s because these types of products may contain a combination of clay-based compounds and fibreglass fibres. Intrusion of the compound’s elements between the seal faces causes separation, damage to the seal faces and creates leakage paths (see Fig.5).
Remember that a film of coolant (micro-gap) must always be present to protect the mechanical seal surfaces from face friction and heat generation.
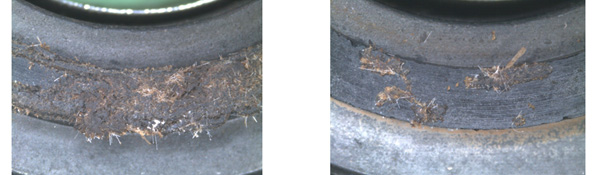
Fig.5
6.Use of liquid sealants
A new WP is usually supplied complete with a gasket. The gasket may be paper, metal, composite or perhaps, a rubber O-ring. The gasket supplied should be the only form of seal between the WP and the engine block. Never use sealant in conjunction with any of them. It is unnecessary, hazardous and will infringe the terms of the warranty, because it will lead to a damaged mechanical seal. The result is continuous leakage and premature failure of the WP.
If gaskets are not supplied and sealant is recommended by the vehicle manufacturer, be sure to use only the recommended size of bead (see Fig 6). Using too much sealant could cause any excess to be sucked inwards, into the cooling system, where it may find its way to the mechanical seal. Premature WP failure is the inevitable result. The sealant no longer acts as a sealant, but as a leakage path. Intrusion of the compound’s elements between the seal faces causes separation, damage to the seal faces and creates leakage paths.
Remember that a film of coolant (micro-gap) must always be present to protect the mechanical seal surfaces from face friction and heat generation.
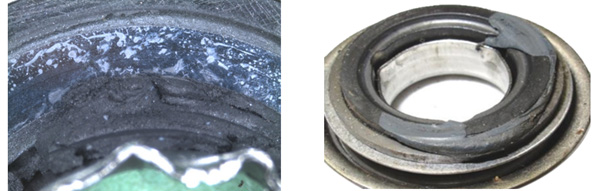
Fig.6
7.Mixing different types of coolant
Intermixing different coolant technologies causes chemical reactions that can produce coagulated
gel-like substances if the silicates separate (fall out) from the coolant solution. This creates blockages in the cooling system.
Automotive cooling systems normally contain a 50/50 mix of distilled, demineralized, or deionized water plus coolant. Don’t use tap water! Most tap water contains chloride, which is corrosive. Tap water may contain calcium and magnesium which can be deposited inside the cooling system, leading to blockages within radiators heater radiator hoses that may also cause WP failure.
Coolant generally contains either ethylene glycol or propylene glycol. The lubricating and cooling properties of the glycol, along with the cooling properties of the water, help to protect the mechanical seal.
See also: https://www.gatestechzone.com/en/news/2021-07-cooling-system-maintenance
8.Good workshop practices:
- Do flush the cooling system properly with a Gates PowerClean (R) Flush Tool 91002
- Don’t rotate the WP manually in dry conditions, only when submerged in new coolant
- Don’t apply sealant to a WP that’s already provided with either a gasket or an O-ring
- Do check expansion bottle and/or radiator for signs of contamination
- Do insist on the use of a good quality coolant as recommended by the vehicle manufacturer whenever the cooling system is being refilled