In years gone by, coolant system checks were generally carried out in the lead-up to the winter period, to ensure the cooling system had been filled with the correct amount of an appropriately coloured-coded antifreeze solution, so that the water within the engine would not freeze, expand and cause damage to the engine components. Today, the situation is more complex. For one, it is no longer best practice to replace coolant simply by colour matching. In what follows, we will explain all about modern coolant technologies and cooling system maintenance, because the use of incorrect or contaminated coolant can cause internal erosion of the engine and the cooling system or other kinds of damage.
Modern coolant technologies
What does engine coolant do?
Coolant used in the automotive industry has three main tasks. Firstly, to prevent fluids within the engine and the cooling system from freezing. Secondly, to protect internal combustion engines and their cooling system components from corrosion. And thirdly, it thus ensures that the oil keeps its lubrification specifications, as well as limiting engine expansion by heat. After all, internal combustion engines burn fossil fuels to generate energy or power, but only about one third of this energy is actually used to move the vehicle. The remaining two thirds convert into excess heat. 50% of that heat escapes through the exhaust system into the atmosphere, while the remaining 50% heats up the engine components. A heat transfer fluid is therefore required to absorb this excess heat retained within the engine. This fluid is circulated through the cooling system, where the heat is transferred to the radiator, which dissipates the heat through cooling fins into the atmosphere.
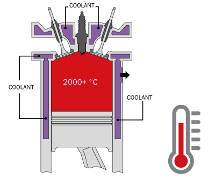
Heat transfer
What does engine coolant contain?
Coolant or antifreeze is generally manufactured using: water (50%), base fluid (45%) and additives (5%).
1. Water
Water is a very effective fluid for transferring heat. Yet it presents potential issues: it has a freezing point of 0 °C and a boiling point of 100 °C, lacks lubricating properties and does not offer protection from corrosion.
Never use hard water in your cooling system. Most tap water contains chloride, which is corrosive, as well as calcium and magnesium which can be deposited, leading to blockages within cooling system radiators and heater radiator hoses, and potentially also causing water pump failure. It is therefore recommended only to use distilled, demineralized or deionized water in a vehicle’s cooling system.
2. Base fluid
The base fluid normally consists of ethylene or propylene glycol. Glycol has good lubricating properties, being especially beneficial to the water pump’s mechanical seal and thermostat valve. Concentrated glycol has a freezing point of approximately -12 °C and a boiling point of 196 °C. A 50/50 mix of water and glycol lowers the freezing point of the solution to around -37 °C while the boiling point of the mixture, at approximately +129 °C, is significantly above that of pure water. Mixing ratios such as 40/60, 30/70 and 35/65 may also be used, depending on the climate. You should always adhere to the coolant manufacturers’ recommended mixing ratios, which are printed on the packaging.
3. Additives or inhibitors
There are many different additive packages or inhibitors that aim to protect the engine and cooling system against corrosion, erosion, cavitation and scale. Additives help to buffer the coolant solution from an acidic pH level to an alkaline pH level.
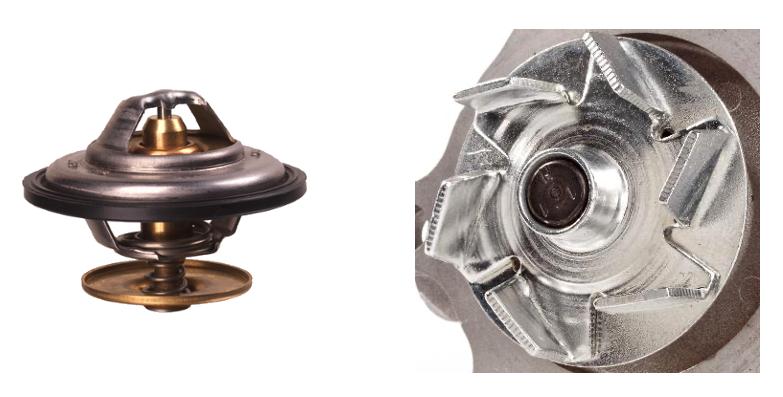
Coolant inhibitors protect components
There are three main classes of coolant technology: Inorganic (Acid) Additive Technology (I.A.T.), Organic (Acid) Additive Technology (O.A.T.) and Hybrid Organic (Acid) Additive Technology (H.O.A.T.).
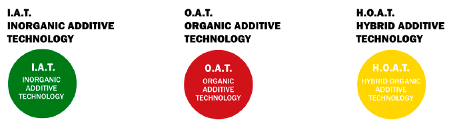
Three main classes of coolant technology
- I.A.T. Inorganic (Acid) Additive Technology
- Suggested lifespan: two years or 30,000 to 40,000 miles (48.280 to 64.373 kilometers).
- These are not acids, but salts of inorganic acids, including silicates, phosphates, amines and nitrites.
- They are the traditional corrosion inhibitors, offering effective protection for all metals and able to lay a protective film over the cooling system components.
- O.A.T. Organic (Acid) Additive Technology:
- Suggested lifespan: five years or 100,000 miles (160.934 kilometers).
- Again, these are not acids, but salts of organic acids, including carboxylates, sebacates, and 2-EHA (2-ethylhexanoic acid).
- These corrosion inhibitors provide specific protection to ferrous metals and aluminum alloys. They do not protect yellow metals such as brass, which use soldered joints. So O.A.T. is not safe for use in older systems that contain brass.
- H.O.A.T. Hybrid Organic (Acid) Additive Technology:
- Suggested lifespan: five to ten years or 150,000 miles (241.401 kilometers).
- This approach involves a combination of IAT and OAT.
Inorganic additives are used to plate cooling system surfaces: they form a thick protective layer but deplete over time. They are not very selective either, which means they cover all surfaces regardless of what material they are made of. Organic additives form chemical bonds with vulnerable surfaces, creating a thin, though extremely stable layer on the areas that need protection.
Maintenance best practices: what to pay attention to
1. Do not mix different coolant technologies
No more colour matching
Green and blue antifreezes used to be dominant, and the general rule was to replace green with new green antifreeze and blue with blue. However, it is no longer best practice to replace coolant simply by colour matching. Today, coolant manufacturers use many different colours but these do not denote the type of coolant technology used in the vehicle’s cooling system.
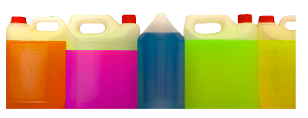
No universal coolant colouring system
The consequences of mixing
Intermixing different coolant technologies having different additive packages can be dangerous. For instance, see the contrasting effects that silicate and borate have on aluminum:
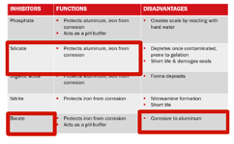
Danger of mixing coolant technologies
Mixing coolants incorrectly can cause a depletion of inhibitors; silicate drop-out; metal contamination; or the appearance of rust and corrosion in the liquid system, leading to component failure. The most common forms of corrosion for aluminum are known as pitting and oxidation; while that for iron and steel is rust.
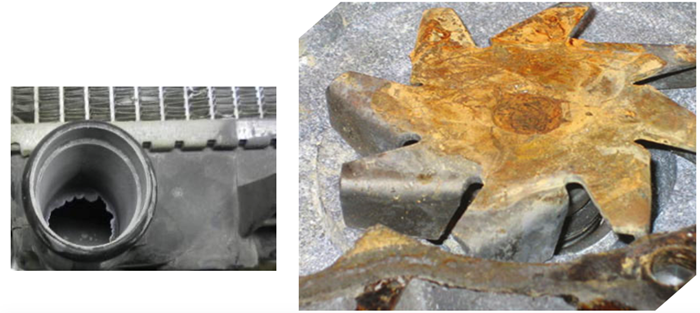
Corrosion of aluminum (left) and iron (right)
Finally, such intermixing can cause chemical reactions. Silicates or phosphates separate from or ‘fall out of’ the coolant solution, depositing a gel like substance in the cooling system (as depicted below). This substance can damage and block radiators, heater cores, water pumps, engine water jackets and cooling system hoses. A mere 2 mm constriction in the narrow parts of the cooling system can reduce system efficiency by up to 40%, due to reduced circulation. Finally, another chemical reaction that may occur is glycol degradation, leading to loss of corrosion protection.
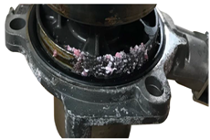
Gel-like substance caused by mixing coolants
2. Check that the coolant hasn’t become acidic/alkaline
Coolant lifespan
As manufacturers of modern vehicles have started to use various different metal types to produce engine and cooling system parts, coolant technology has had to evolve to incorporate appropriate system protection. As coolant ages, the protective inhibitors are used up or ‘drop out’ of the solution. So, the longer the coolant is left, unchecked, in the cooling system the higher the chances of it becoming acidic. And an acidic solution will obviously cause internal erosion to the engine (and its metal components) and to the cooling system. Acid reacts with metal surfaces, causing deposits to form within the cooling system. These deposits can also be transported and deposited throughout the cooling system, restricting flow and causing overheating.
Undetected leaking head gasket
Furthermore, it does not suffice just to keep an eye on the lifespan that is indicated on the coolant packaging. This lifespan can be shortened as a result of various factors, such as an undetected leaking head gasket. Combustion gasses leaking from the combustion chamber into the engine waterways mix with the coolant and cause it to become acidic. Therefore, it is recommended to carry out regular cooling system pressure checks during scheduled maintenance, for example, by using the Gates Cooling System Pressure Tester 31367.
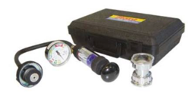
Gates Cooling System Pressure Tester 31367
Bad earthing point between engine and chassis
Another common cause of the premature failure or loss of cooling system inhibitors is a bad earthing point between the vehicle engine and chassis. Bad vehicle earthing points can cause electrical current to take an alternative route back to the battery, for instance via the coolant in the system (which then becomes a conductive electrolyte). In the case of such a galvanic reaction, the inhibitors are rapidly consumed from the coolant solution, causing the fluid to become acidic.
Visible signs of a galvanic reaction within a cooling system include dark, uneven discolouration of the internal metal surfaces of the water pump. These discoloured surfaces have a slightly gritty feel.
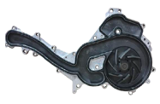
Water pump discolouration due to galvanic reaction
Yet, as the damage is not always immediately visible, you should use a multimeter to test the coolant for the presence of voltage.
- When the engine is at normal operating temperature, position the negative (-) probe on a good earth point and the positive (+) probe directly in the coolant in the top of the radiator or expansion bottle. Be careful: there is pressure in the system when at operating temperature.
- Do not allow the positive probe to touch any metal parts (if present).
- Increase the engine speed to approximately 2,000 rpm.
- If the meter reads less than 0.3 volts, the coolant is in good condition.
- If it reads 0.3 volts or more, the inhibitor additives are depleted and are no longer protecting the cooling system.
- Find the cause of the current flow.
- Check and replace any faulty or damaged earthing straps or cables.
- Ensure the earthing points are clean and protected from the elements.
- Flush the cooling system using the Gates Power Clean Flush tool 91002.
- Immediately replace the coolant with the coolant type recommended by the car manufacturer.
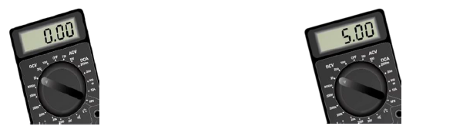
Check coolant for the presence of voltage with a multimeter
Measure pH level to check coolant’s acidity or alkalinity
A pH test meter or pH test strips should also be used to check the pH of the coolant to monitor the condition of the additive package.
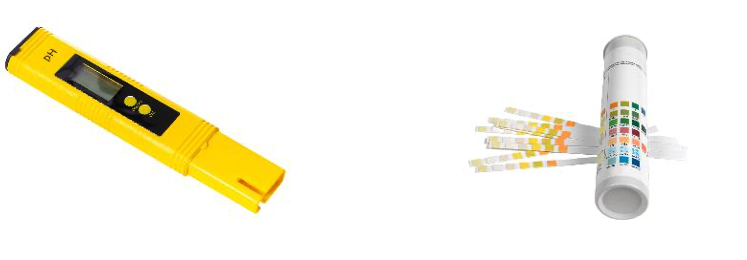
pH meter and pH strips
pH is an indication of the acidity or alkalinity of a fluid. Coolant generally has a pH range between 8.5 and 10.5. If the pH is too low, the coolant has become acidic and will begin to attack both aluminum and ferrous materials like iron and steel. If the pH is too high, the coolant is excessively alkaline and will attack non-ferrous materials such as copper and aluminum.
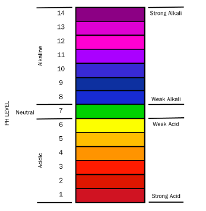
pH chart showing degrees of acidity and alkalinity
3. Check the freezing point
The coolant freezing point should also be checked regularly, especially at service maintenance intervals. Hydrometers are no longer the approved equipment for coolant testing. A refractometer is now used: the Gates Refractometer (part number 91001) can be used both for testing glycol concentrations in cooling systems and for measuring the state of charge and specific gravity of the electrolyte in lead-acid batteries.
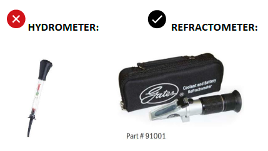
Appropriate tool for checking freezing point
4. Perform a complete flush and refill
When carrying out repairs on the cooling system, you should:
Flush the system completely, using a Gates Power Clean Flush Tool (part number 91002).
Fill the system with the correct coolant or antifreeze. Dilute the correct coolant type with water until you get a 50/50 mix, or use a prediluted coolant mixture of the correct coolant.
Bleed the system to ensure it is entirely free of air. (Modern systems may require diagnostics equipment to bleed them correctly.)
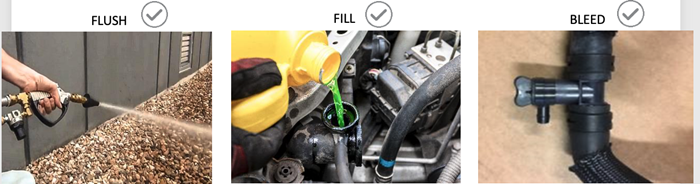
Best practice procedure
This is crucial to avoid contamination and the problems discussed above. Keep in mind that a coolant change is less expensive than having to replace cooling system components like radiators or heater cores. Moreover, most coolant packaging labels state that the coolant’s five or ten years guaranteed corrosion protection is only valid when a complete cooling system flush and fill is performed.
The importance of a clean cooling system
Although Gates is not a coolant manufacturer, we do manufacture and supply coolant system components that may be damaged by the use of incorrect or contaminated coolant. So we would like to conclude by listing the benefits of a clean cooling system, which enables:
- more efficient engine cooling
- quicker engine warm up
- better fuel consumption
- longer lasting components
- reduced comebacks
- increased customer confidence