Electric water pumps have been around for many years now. However, prior to the last decade, they have not often been a particular center of attention. That situation has changed completely, though, as electric water pumps have become ever more indispensable in keeping the cooling system functioning optimally, both in combustion engines and hybrid and electric vehicles. In what follows, we will trace this evolution by zooming in on the
various uses of electric water pumps – both main water pumps and those responsible for the thermal management of vehicles (from turbocharger system cooling to battery cooling). We also introduce the most important
pump components.
The main uses of electric water pumps
Taking a look at the main uses of electric water pumps is one of the best ways to understand how they have evolved.
Programmable additional heating
Programmable additional heating was one of the first applications to feature electric water pumps. In such systems, an additional heater uses the vehicle’s own fuel to heat coolant to the temperature required to warm up the passenger compartment. This not only guarantees that the compartment is at a pleasant temperature when the car user gets in; it also means that the engine starts to operate at an optimal temperature, reducing wear on the corresponding parts. In most cases, the climate control unit controls both the additional heater and the electric water pump, so that any residual heat present in the cooling system can be used to ensure continued heating even after the engine has been turned off.
Electric water pump
Pumps supporting the cooling system
Cooling systems have become more and more complex as vehicle manufacturers continue to improve car performance. Nowadays, these systems require not only modular hoses, but also electric water pumps in order to work independently of the coolant flow provided by the main mechanical pump, or even to operate in completely separate circuits.
Avoiding overheating and prolonging component life
The first to appear on the market were electric pumps that, after the engine has stopped, continue pumping coolant for a while. By lowering the engine temperature, they avoid overheating and prolong the life of its components. They work in a similar fashion to additional heating pumps, as in some cases the passenger compartment continues to receive heating for an additional time after the engine has been turned off.
Thermal management system
These days, the cooling system has become the thermal management system of many vehicles, where the engine control unit manages all the elements and decides how to respond in order to keep every component at the right operating temperature.
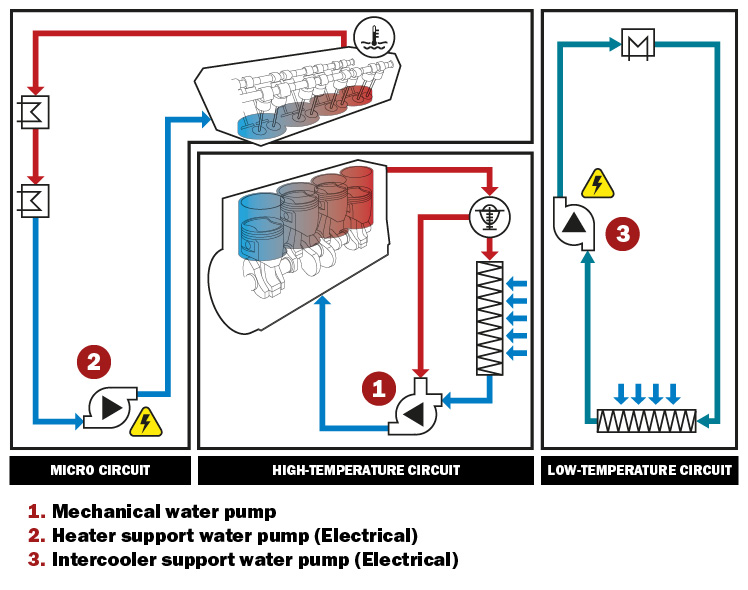
In the context of thermal management, it is important to highlight micro-hybrid vehicles equipped with Stop & Start systems and other hybrid vehicles. To maintain the flow of coolant to auxiliary elements such as the turbo or the cabin heating system despite frequent stops and start of the engine, they rely on an electric water pump. Thus, the pump prolongs the turbo’s service life and avoids premature breakdowns, as well as ensuring that the passenger compartment continues to receive hot air as necessary.
In addition, we have seen a growing trend towards cooling the gases compressed by the turbo or compressor using an intercooler that operates, using coolant rather than on outside air. Those gases need to be cooled to increase efficiency: as hot air has a lower density, it will contain less oxygen for the engine to burn. When these gases are cooled, the density and hence the oxygen level increases, resulting in a more powerful engine.
Water pump 41554E
Some modern electric vehicles even have up to four electric water pumps to take care of their thermal management.
Electric vehicle with electric water pumps
Main water pumps
Electric main water pumps result in less fuel usage than do their mechanical counterparts since the latter constantly consume energy from the engine because they are continually in motion, being moved by the timing belt or the accessory belt. So, replacing a mechanical pump with an electric pump that can be activated according to the actual needs of the engine can result in a significant reduction in fuel consumption.
In the engine warm-up phase, for example, the control unit can decide not to activate the water pump at all, in order to allow the service temperature to be reached sooner. In our article on electrically controlled thermostats, we saw how the 41504E water pump fitted by BMW can increase or decrease the flow rate of the coolant and adapt the coolant temperature to the driving style.
Water pump 41504E
Pump components
Over the years, not only has the use of electric water pumps changed, the technology they rely on has been transformed as well. The first types of electric water pump to be used were traditional DC pumps with brushes or electrical contacts to conduct electrical current between stationary and rotating motor parts. Now, that trend has changed, and brushless motors are more widely used.
A motor with brushes vs. a brushless motor
Although there are many different designs, the composition of the various water pumps is very similar. The main parts are:
- Impeller/Rotor: this part is responsible for moving the coolant using a rotor that features drive blades. Internally, this rotor contains the permanent magnets necessary in a brushless motor to generate the rotating movement.
- Body/Stator: this part generates magnetic fields through the windings to make the rotor rotate.
- Control unit: this unit transforms the received direct current into three-phase current that is transmitted to the estator. Thanks to a Pulse Width Modulation signal (PWM), the Printed Circuit Board (PCB) knows the speed at which the pump has to rotate (though some pumps are controlled by the vehicle’s data bus).
The main components of an electrical water pump
Failure modes
To learn about the most common failure modes, please see our article on the unique characteristics of electric water pumps and the main causes of their failure.
These newer pumps are monitored and generate a fault code when if control unit detects an issue, but as always, it is advisable to check the wiring diagram:
- Power cable (check the voltage to make sure there is full battery power (12 to 14.8V))
- Ground wire (measure ground resistance)
- Signal/data bus cable to the control unit (the resistance between the electric water pump connector and engine control unit should be lower than 0.4 ohms)